O prazo para entrega dos produtos da sua empresa tem sido muito longo diante do que o seu concorrente tem oferecido? Sua empresa acumula muitos estoques flutuantes entre as operações? O que você gasta operacionalmente está alto e isso tem feito você considerar que sua empresa pode estar perdendo competitividade no mercado?
Se estas são algumas das perguntas que você costuma se fazer, talvez esteja na hora de você buscar uma boa solução para melhorar os processos internos nas etapas de produção.
Entendendo o que é fluxo contínuo?
Existem alguns métodos fundamentais e ideais para alcançar estes objetivos de forma precisa, como é o caso da implantação de um fluxo contínuo, um dos princípios de qualquer processo lean. A metodologia propõe a produção apenas do que é exigido pelo processo seguinte, ou do cliente final, dependendo da empresa a qual se refere, impossibilitando, assim, que estoques sejam gerados entre os processos, reduzindo o lead time e o work in process, além do aumento significativo do atendimento ao prazo do fluxo de valor completo.
De onde surgiu o fluxo contínuo?
Mesmo ainda sendo um método muito atual e presente em várias empresas, o conceito de produção em fluxo não é recente. Em 1910, Henry Ford, fundador da Ford Motor Company, foi o primeiro empresário a aplicar o conceito no início da industrialização nos processos produtivos de veículos em massa. Aplicando a montagem em série e em movimento, ele desenvolveu uma metodologia, conhecida hoje como produção enxuta, capaz de fazer seus funcionários produzirem em menos tempo e a um menor custo. Com a padronização que o novo sistema nos processos de produção propunha, carros que antes eram produzidos em 12,5 horas passaram a ser montados em apenas 93 minutos.
Com maior produtividade e consequente aumento no lucro, o sistema em fluxo da Ford revolucionou a sociedade industrial com conceitos sobre o modo de se produzir que se arrastam até hoje, na comprovação irrefutável de que a organização de uma indústria, seja na esfera administrativa ou diretamente no chão de fábrica, é determinante para o alcance do máximo de produtividade e consequente sucesso de todo e qualquer negócio. E é exatamente sobre essa metodologia organizacional nos processos produtivos a que se refere o chamado fluxo contínuo.
Fluxo contínuo serve para a minha empresa?
Aplicável em todo lugar em que haja a necessidade de divisão, organização do espaço e fluidez de pessoas ou materiais, o fluxo contínuo serve para qualquer empresa. A proposta é interessante sob o ponto de vista da organização que seja pertinente às especificidades do negócio, conduzindo a redução de etapas, esforços, tempos e custos que sejam desnecessários e refletem negativamente no faturamento.
Como a Produção Enxuta pode reduzir os custos da sua empresa?
Através de uma metodologia, o fluxo contínuo, aplicado em um layout, propõe a organização nos processos de produção, reduzindo esperas, acúmulo de estoques em processos, eliminando filas e trabalhando exatamente de acordo com o ritmo da demanda da empresa.
Basicamente são quatro os tipos mais comuns de layout utilizados em fluxos contínuos e eles coabitam o mesmo cenário. Isso porquê, a escolha de um arranjo operacional (layout) ineficiente prejudica a fluidez do processo, aumentando custos operacionais, de transporte e movimentação. Tornando, assim, a gestão mais trabalhosa, níveis excessivos de estoques em processo e resultados prejudicados.
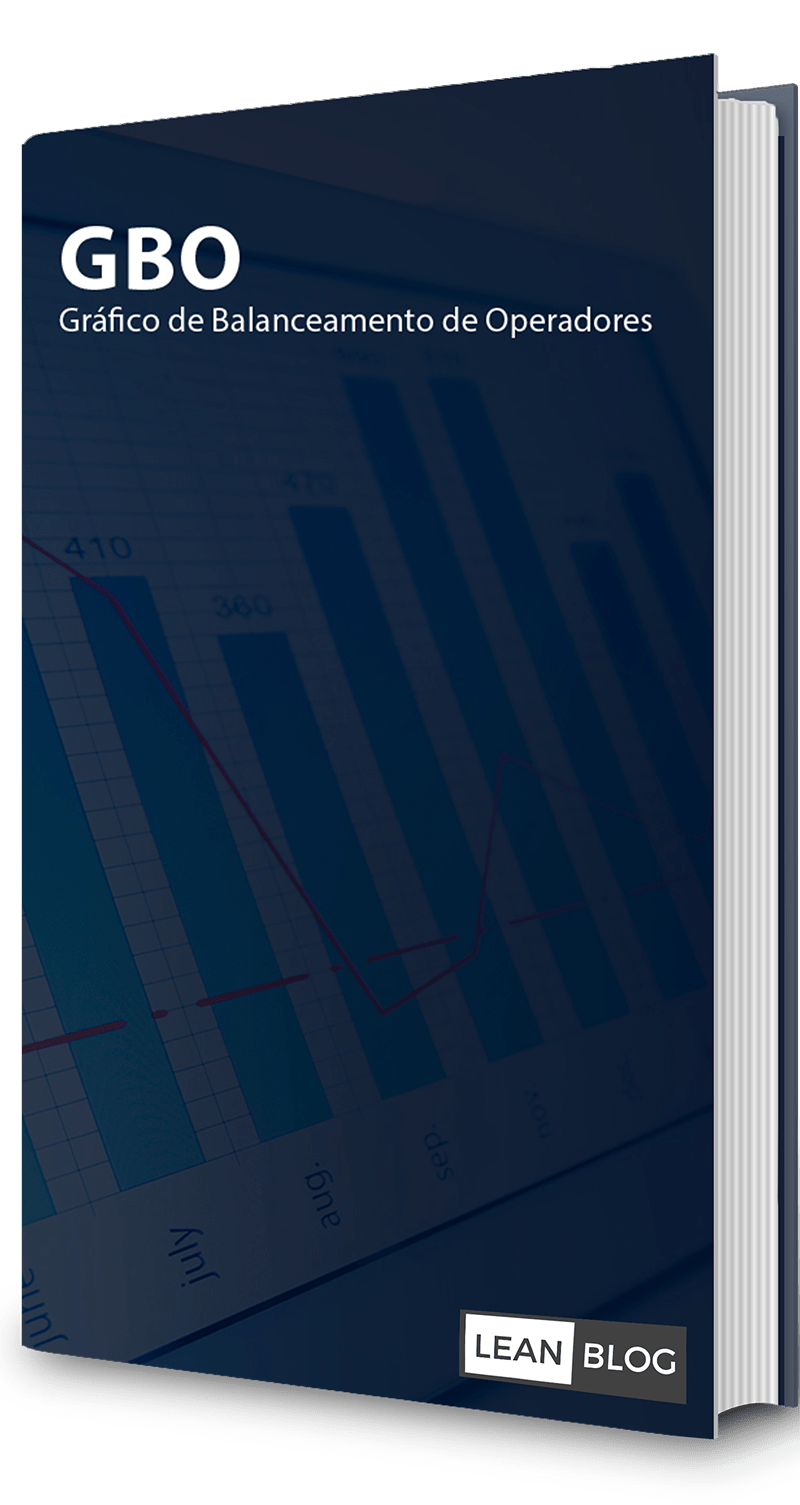
Acesse o ebook gratuito
GBO – GRÁFICO DE BALANCEAMENTO DE OPERADORES
Conheça os layouts mais comuns do fluxo contínuo:
– Layout por posição fixa ou posicional
Interessante para empresas que trabalhem com produtos de grandes dimensões, cujos processos de produção não podem tirá-lo de determinadas posições e são os funcionários e os maquinários que operam em movimentação ao redor do produto. É um formato organizacional para empresas de alto valor agregado e baixa produção em termos de quantidade, como construção de aviões, edifícios, estradas, entre outros.
– Layout por processo ou funcional
Funciona para empresas cujos processos e equipamentos das mesmas operações são agregados em uma única área, utilizado comumente em produções intermitentes, com grande variação de peças e lotes. Como exemplo, apenas a nível de ilustração, ainda que fora de um setor fabril, podemos analisar o processo como sendo um hospital ou um supermercado, locais onde o cliente (que seriam os ‘funcionários’) é direcionado para o setor escolhido (que seriam os maquinários e/ou equipamentos) a partir da sua necessidade.
– Layout em linha ou por produto
Comumente utilizado em fábricas e empresas cujos maquinários e as estações e trabalho são dispostas conforme as etapas do processo de produção, sem que o fluxo produtivo tenha caminhos alternativos, isto é, precisa passar, necessariamente, por cada etapa da operação. O layout é oportuno em empresas cujos processos de fabricação ou de montagem são padronizados, como indústrias com baixa variedade de produtos e processos padronizados, como a indústria automobilística, por exemplo.
– Layout celular
Muito utilizado em empresas com produção em massa onde haja padronização de processos e etapas. Este layout se propõe a dividir o sistema produtivo em células que concentrem todos os maquinários e ferramentas necessários para a produção de determinado produto. Todas estas células funcionam como subsistemas auto-suficientes e auto-gerenciáveis.
Para saber mais sobre Layout de produção, veja também este artigo!
Independentemente de qual destes modelos se encaixa melhor dentro da cadeia produtiva da sua empresa, a eficiência do fluxo contínuo depende de métodos estruturados que avaliam diversos conceitos de melhoria contínua, como o Takt Time, tempo, estabilidade e capacidade dos processos. Por isso é tão importante que a implantação seja estruturada por profissionais qualificados.
A Terzoni proporciona boas alternativas de capacitações, consultorias e soluções para tornar o fluxo contínuo uma realidade dentro da sua empresa. Entre em contato conosco e saiba como podemos ajudá-lo!
Você pode se interessar por esses outros conteúdos sobre LEAN!
[…] assim, o balanceamento de linha de produção objetiva restabelecer o fluxo contínuo, eliminando permanentemente os desperdícios como tempo de espera em […]
[…] implantação de um fluxo contínuo propõe que seja produzido apenas o que é exigido pelo processo seguinte, ou do cliente final, […]
[…] 5s é organizar o ambiente para que os processos se tornem mais simples e a produção tenham um fluxo contínuo. O resultado é maior eficiência na […]
[…] aqui que o fluxo deva ser contínuo, percorrendo cada etapa de maneira fluida e eficaz para o melhor valor […]
[…] Passo 5: Procure por um fluxo contínuo. […]
[…] são prejudicados e ocorre o desperdício de tempo produtivo. Portanto, é necessário garantir um fluxo contínuo de atividades para evitar esse tipo de […]
Parabéns pela ótimo artigo, muito bom seu trabalho.
Obrigado Gustavo!
Quero parabenizar você pelo seu artigo escrito, sou Kamila de Oliveira e gostei do seu site, muito bom vou acompanhar o seus artigos.
Obrigada Kamila! Se inscreva também em nossa newsletter para saber das novidades. 😉